Shaft End Technology & Torque Monitoring
Riverhawk provides intelligent hydraulic mounting tools to assist with installing and extracting adaptive hardware such as flexible coupling hubs, gearwheels, and thrust discs.
Such hardware in the past would have used the heat in the form of a flame-torch (not recommended), a heated oil bath, or an electric heating coil. Besides being cumbersome and difficult to use, they were a health and safety risk.
Riverhawk is one of the leading manufacturers of hydraulic equipment for GE, Nuovo-Pignone, Siemens Dresser-Rand and other turbo-machinery OEM’s. The equipment offers end-users such as Aramco, ExxonMobil, Shell, Woodside and many others the benefits of:
- Easy method of installation and removal
- Accurate control of interference fit and therefore torque transmission
- Conformance to relevant engineering standards ie API 671 and ISO 10442 requirements
- Health & Safety benefits
Hydraulic Pusher Tools for Hub Installation
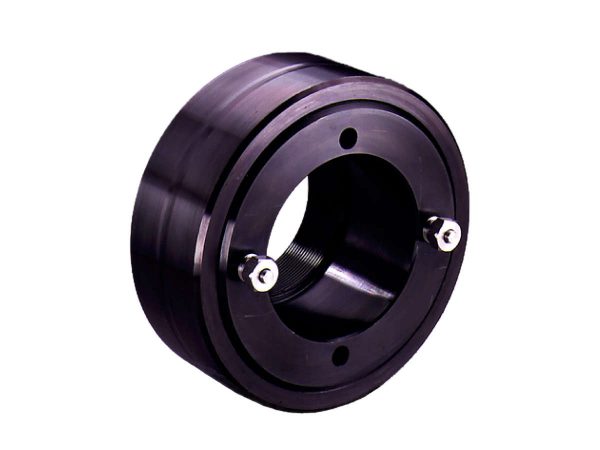
Riverhawk's engineers designed the hydraulic pusher tools to suit a wide range of shaft end to coupling hub configurations. The tools offer bespoke features and fine-tuned designs using FEA for a minimum weight and excellent stress distribution.
The Hydraulic Hub Pusher installation tool provides:
- A design based around a Riverhawk standard but tuned to match the clients’ machinery shaft ends
- The ability for a full stroke to accommodate the whole hub ‘pull-up’ range
- Heat-treated alloy steel for durability and regular use
- Tool assemblies that are tested to ensure they are leak-proof during use
- Complete assembly in a rugged case along with and relevant accessories and fittings
Hydraulic Puller Tools for Hub Removal
Riverhawk Hydraulic Hub Pullers are engineered to assist in the removal of coupling hubs in an effective and safe manner.
The Hydraulic Hub Puller tool provides:
- A design based around a Riverhawk standard primarily for the removal of parallel bored coupling hubs
- The ability to be used to hydraulically assist the removal of ‘tapered and keyed’ coupling hubs
- A full stroke extension to accommodate a wider coupling hub ‘pull-up’ range
- Heat treated alloy steel for durability and regular use
- Thread-in adaptive hardware for shaft port applications
- Tool assemblies that are tested to ensure leak-proof during use
- Complete assembly in a rugged case along with and relevant accessories and fittings
Hydraulic Shrink & Clamp Disc
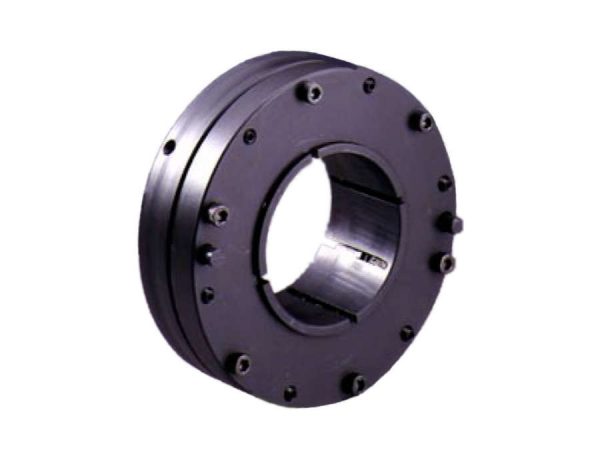
The Riverhawk Hydraulic Shrink & Clamp Disc is the modern method to secure coupling and other transmission devices' adaptive hardware to shaft ends. The disc features infinite adjustment with slip-fit components for ease of assembly, and it provides clamping of adaptive hardware with total-integrity.
The disc further enables a reduction in boss diameter, shorter interface and in most cases, lower weight and lower overhung moment.
Additionally, the Riverhawk design helps to reduce costs:
- Due to the elimination of keys, splines that cause stress concentrations in machine shafts and tapered shaft ends which are expensive to manufacture.
- By providing the ability to accommodate a damaged shaft end rather than manufacturing a complete new shaft.
In summary, the Hydraulic Shrink & Clamp Disc provides:
- A ‘slip-fit’ component for keyless connection
- A reduced cost solution due to the elimination of keys, splines and tapered shaft ends
- An excellent solution for the repair of a damaged shaft end
- A hydraulically applied high clamping pressure for high torque transmission
- The ability to use a smaller shaft diameter resulting in a reduced overhung moment design
- The ability for custom designs.
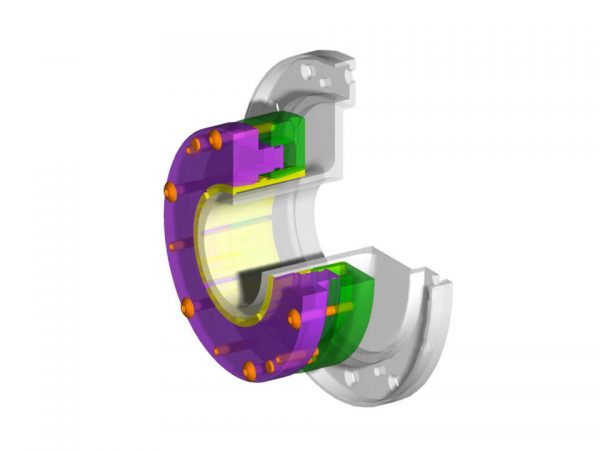
Taper Ring, Plug Gauge and Lapping Tools
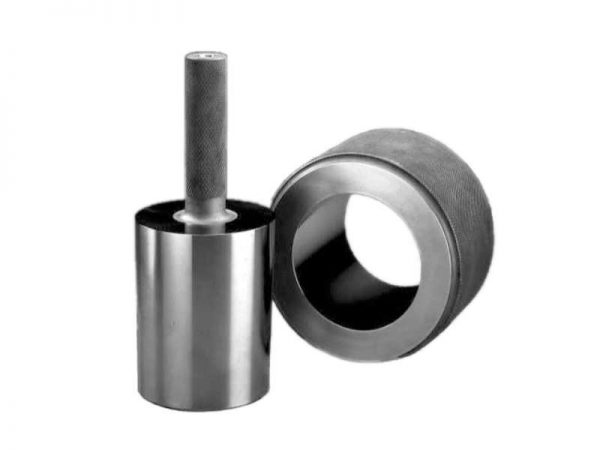
Standard range or bespoke Taper plug and ring gauge sets are available. The tools come with certification and feature material traceability and calibration traceability to National Institute of Standards and Technology (NIST). They also comply with the API 671 and ISO 10442 requirements.
- A design based around a Riverhawk standard but tuned to match the clients' machinery shaft ends
- A taper contact area of min 90% to 95% and guaranteed with blueing tapes documented and held on file (scanned copy provided in certification report)
- Conformity to API 671 and ISO 10442 requirements
- Use of the highest quality tool steel used, typically AISI A6 Tool Steel and ASTM A276 440C Stainless Steel
- The Minimum hardness of Rockwell C 58 (HRC)
- Calibration, material traceability and certification
Lapping Tools
The lapping tools are cross-matched with the corresponding taper ring and plug gauge set to provide a Minimum 90% taper contact area guaranteed taper contact.
The lapping tools provide a method of correcting a taper that is 'out-of-tolerance' to the existing shaft and hub surfaces.
- Manufacturing from ASTM A48 cast iron material
- The ability to be machine matched to existing tapers
- Conformity to API 671 and ISO 10442 requirements
- A minimum 90% taper contact area guaranteed with blueing tapes documented and held on file (scanned copy provided with certification report)