Dedicated Filtration
While one may have heard or read numerous times that new oil is not clean oil, it is surprising how many installations lack proper filtration equipment for pre-filtering or continuous filtration of dirty processes or environments.
Whether continuous on-line or of the off-line 'kidney-loop' type, permanent filtration system solutions provide long-term optimisation of fluid cleanliness for machinery difficult to access or expensive to maintain.
RO-QUIP supplies a number of filtration system brands that offer many features:
- Addition of Particle Monitoring Instruments
- Explosion-proof models
- A range of power option
- Stainless steel towers
Featured Filtration Partners and Products
Click the arrows for the brands below to see the featured models
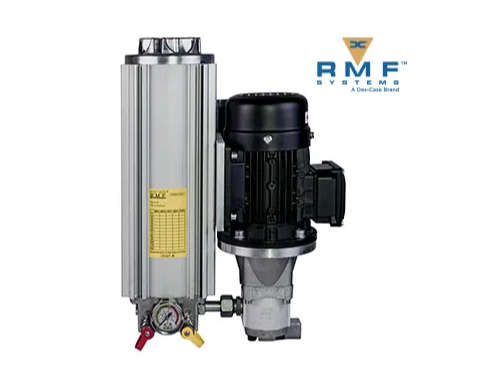
Off-Line Filtration Unit
It is commonly stated that 80% of hydraulic failures are caused by contamination in the system. Whether it is so high today is not clear. Still, it's a fact that contamination starts right at the lubricating oil production through the various stages of transfer, i.e. supply chain, and into the machinery.
The Off-Line Units remove that contamination build-up and continue to do so through system operation, removing it at the source. These systems are also capable of removing water.
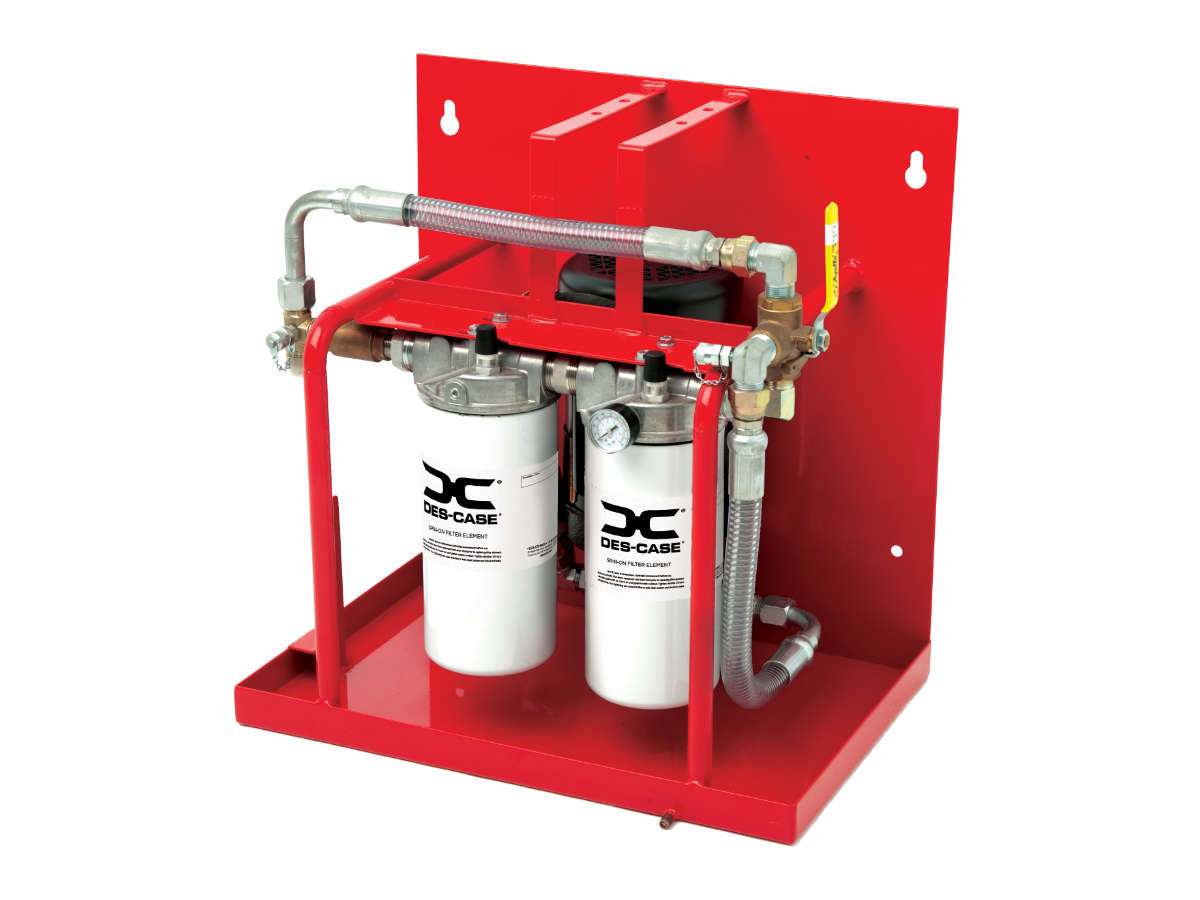
Panel Filtration Unit (Off-Line)
The Panel units with low flow rates are an excellent choice for mineral-based oils in small to medium-sized reservoirs. Whether you have an application that needs regular filtration, or a maintenance workshop cum work area where you bring equipment to be filtered, the panel unit is a modular solution, mountable where you need it the most.

Cleaner fuels lead to better combustion, longer injector life and lower engine wear rates resulting in lower fuel consumption, improved reliability and ultimately higher profitability and lower emissions.
Such benefits mean a Diesel oil conditioning system is an essential purchase for mine operators, mobile vehicles, marine vessel fleets, and the 'internet world' Data centres relying on emergency diesel-powered generator backup units.

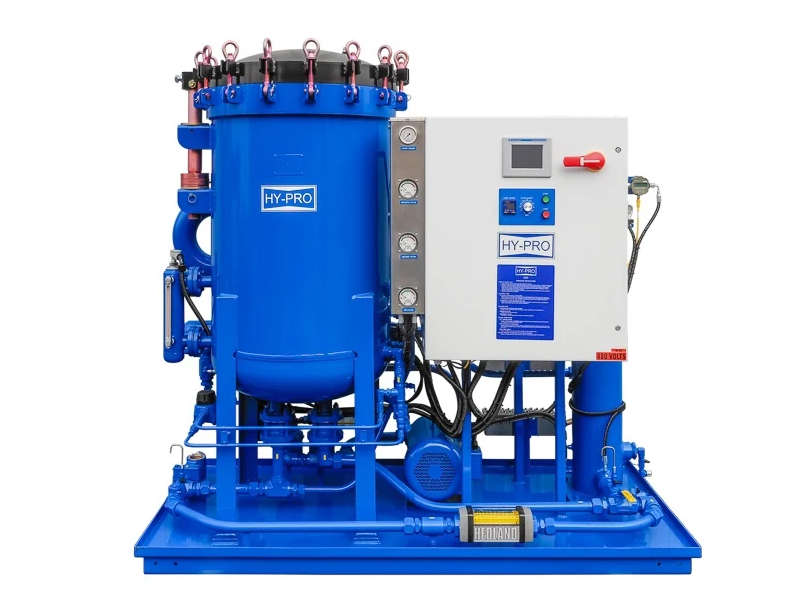
Turbine conditioning systems prevent the accumulation of oxidation material, maintain consistent lubricant purity as well as eliminate typical performance issues such as varnishing and high rates of additive loss.
Minimise additive consumption and manage as well as extend lubricant life with an annual top-up strategy using the same lubricant brand. This is a low-risk approach with predictable costs and results. In this case, the COT skid combines high-efficiency single pass particulate and water removal coalescing technology to guarantee that the turbine oil is always is within specification.
We offer:
- Particulate media options down to β2.5[C] > 1000 and 100% synthetic coalesce/separator elements that remove all emulsified and free water down to saturation point
- Oil sample valves to enable you to consistently and accurately monitor your critical turbine lubricating oil condition and the filtration system performance.
Thus, premature component failures and resulting expensive downtime are eliminated providing optimum turbine operation, performance and reliability.
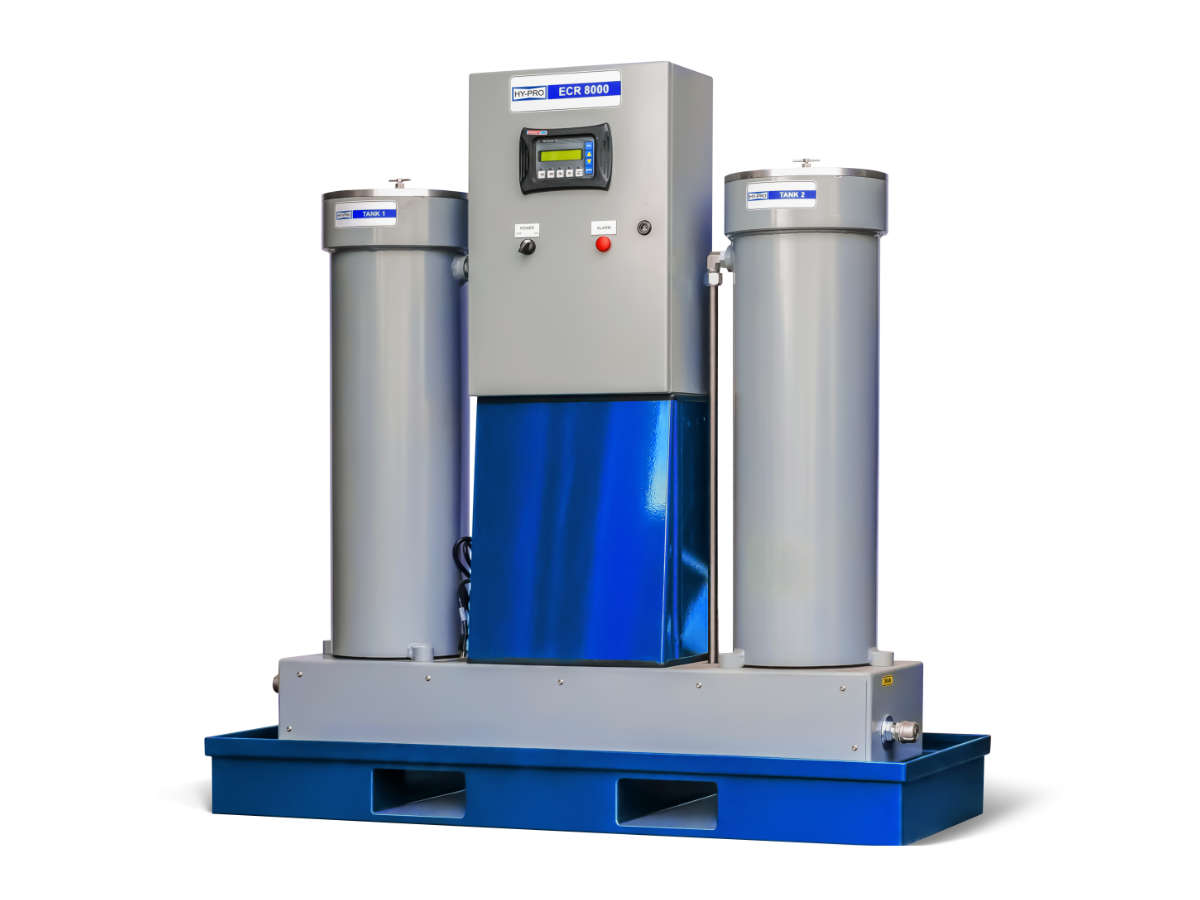
Hy-Pro specifically designed the system for sub-micron insoluble contamination removal, common in phosphate ester fluids and turbine EHC systems, to extend the oil life.
The system removes fine particulate that is below the removal capability of mechanical particulate filters. It differs from the standard Electrostatic Oil Cleaner systems, which are ineffective for phosphate ester fluid applications because of fluid conductivity restrictions.
ECR™ improves fluid colour and reduces solid contamination levels significantly. Use ECR™ in conjunction with ICB™ for acid and dissolved contamination removal and TMR-N2™ for water removal to achieve comprehensive fluid maintenance and even over time eliminate the need for chemical flushes.
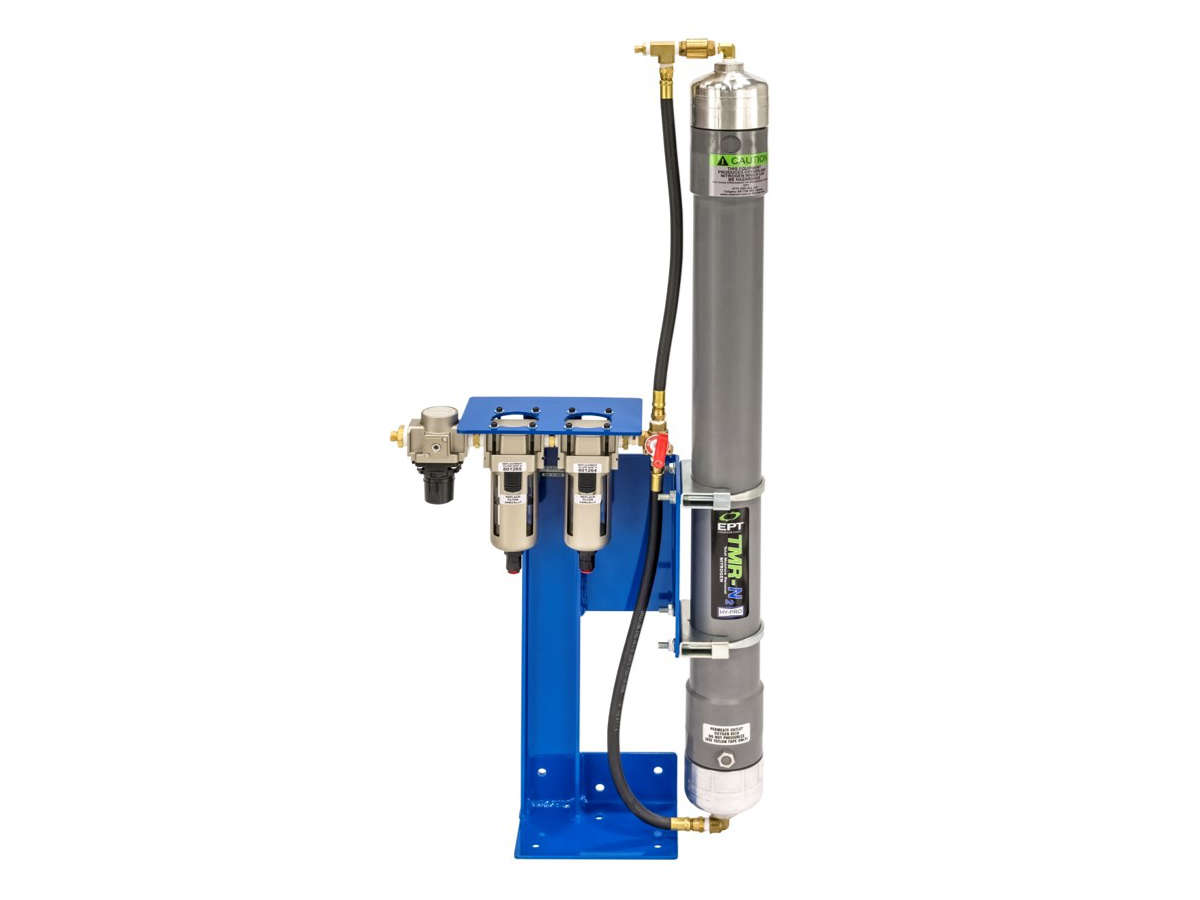
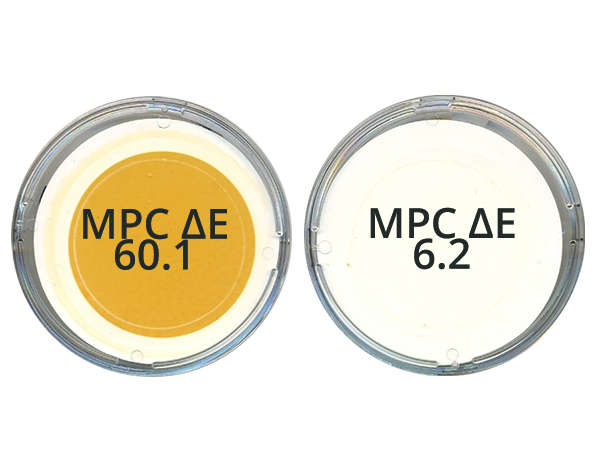
MPC Varnish potential patch testing (ASTM D-7843)
Micro-dieseling and filter element spark discharge generate sub-micron insoluble hydrocarbon particles that cannot be removed by traditional particulate filtration.
Using a high voltage electrostatic field with a special collector element, sub-micron particles are removed (ie the cause of dark EHC fluid and high varnish potential readings (MPC) as seen in the MPC patch test results).
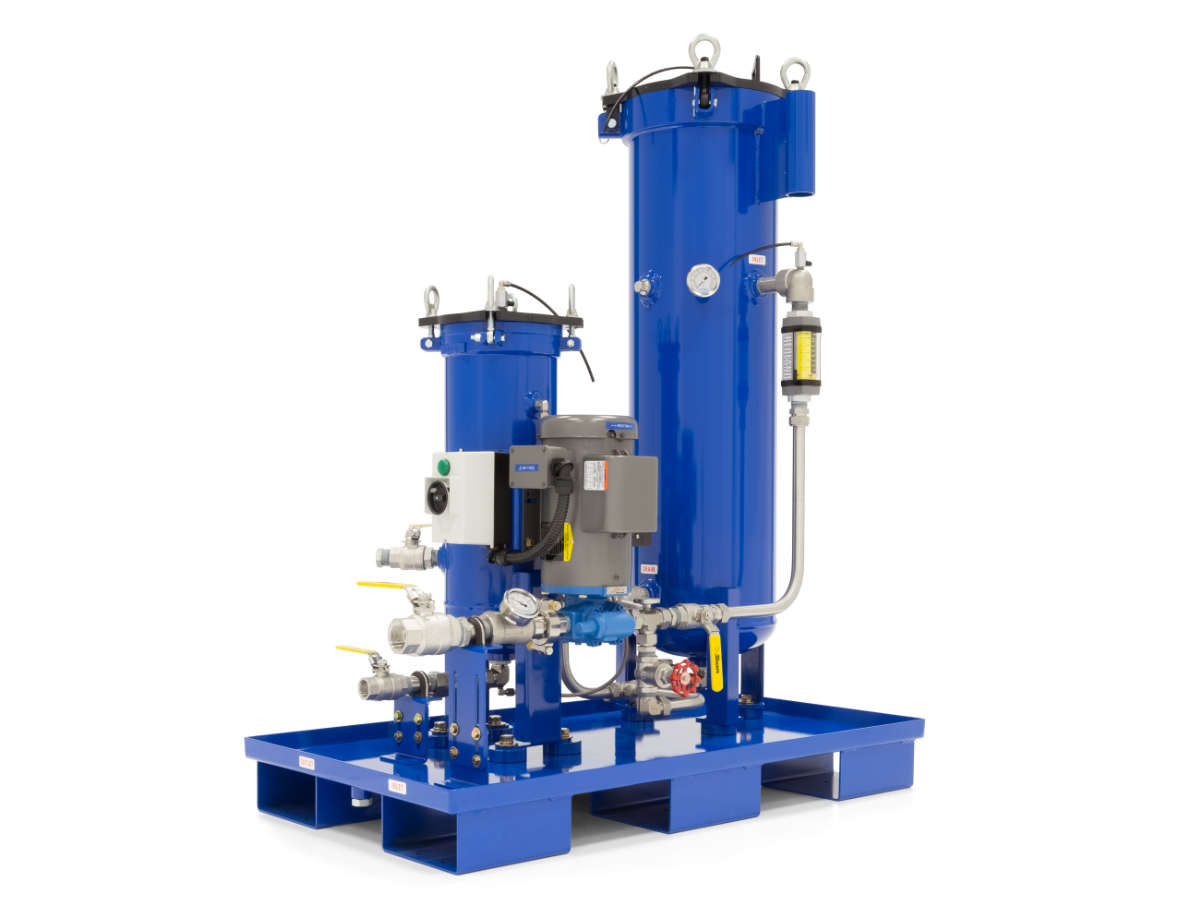
The ultimate and proven complete recovery and maintenance solution for EHC (i.e. phosphate ester fluids) and mineral-oil based lubricants for turbines and compressors.
SVR removes the waste oxidation by-products that can lead to varnish formation, thus restoring the oils original solvency properties forcing all insoluble deposits to be dissolved back into the oil for removal. Further, a dedicated SVR system works in parallel with Anti-Oxidant (AO) additives to slow depletion, thereby dramatically extending oil life.
Ion Charge Bonding (ICB™) with advanced resin technology is used to remove the soluble by-products and restore demulsibility during regular operation without damaging the additives' chemistry.
Combining the ICB™ technology with high-efficiency VTM particulate media removes insoluble by-products. This will deliver very low ISO cleanliness codes keeping the in-service oil or phosphate ester fluid clean and longer than ever before.
Purchasing the SVR system also comes with comprehensive oil analysis and a results interpretation package from a leading independent lab and industry experts in industrial turbines to provide the best solution to extending your fluid life.
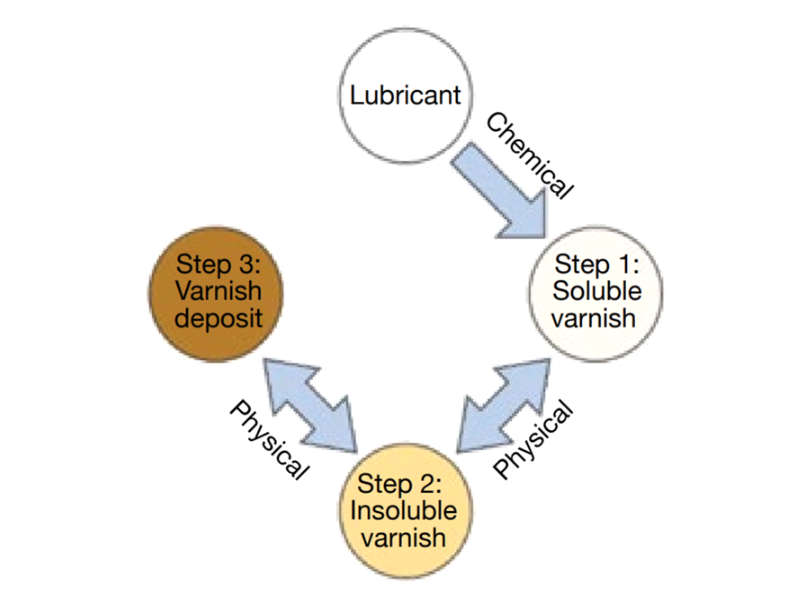
The Varnish Formation Cycle
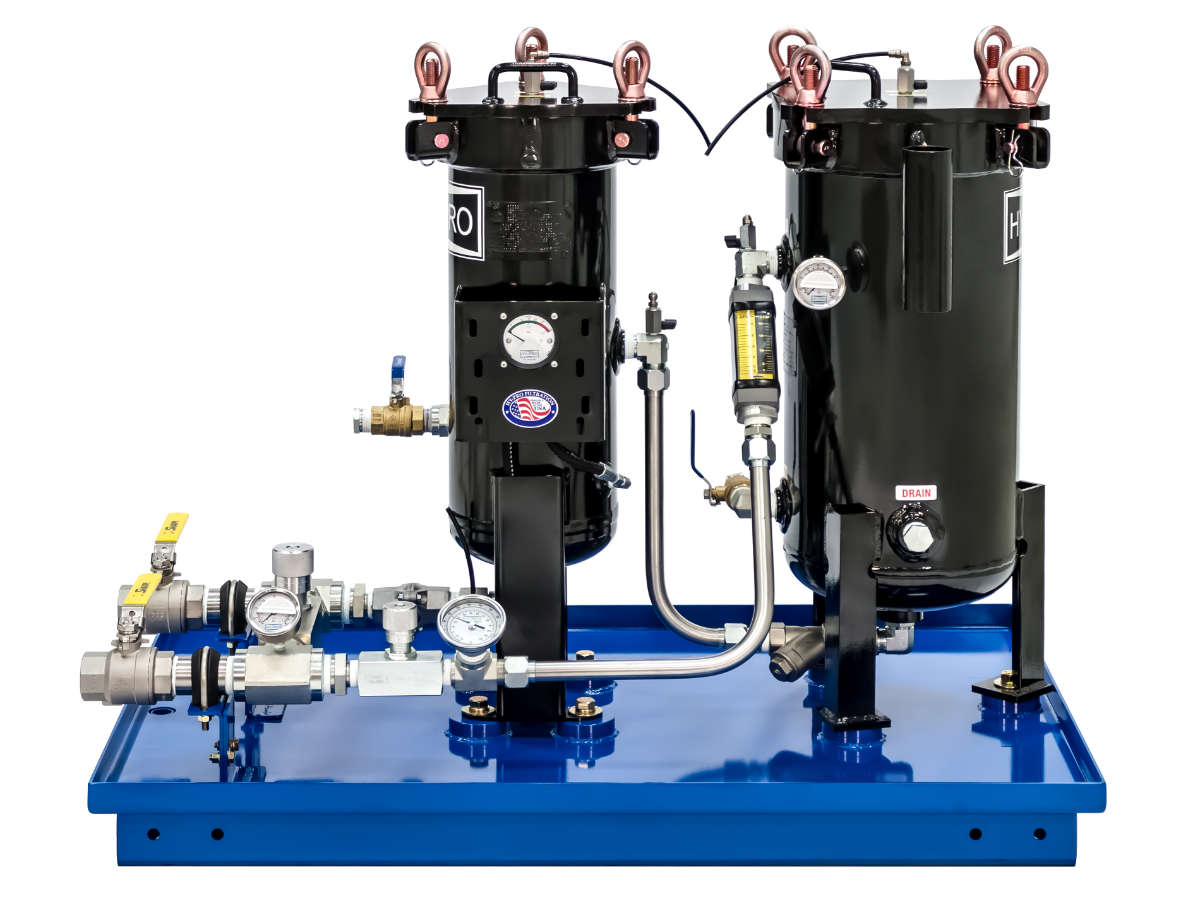
The FSTO oil conditioning system combines the ICB technology with high-efficiency VTM media for turbine and compressor lube oils. For smaller reservoir capacities or lower flow rates, FSTO systems can be adapted.