Riverhawk Hydraulic Nut
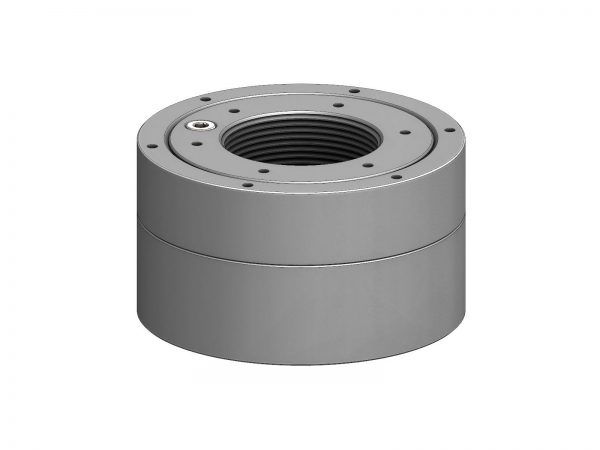
The design of the Riwerhawk Hydraulic Nut avoids bolt load torque inaccuracy from stud twisting as well as friction loss at the thread interfaces and nut face. The nut's compact size makes it an excellent choice where space is confined or when faced with envelope restrictions.
Even when tensioning multiple connected nuts, the Riwerhawk Hydraulic nut maintains a uniform compression of flanges, bearing houses, casings or connection rods.
Riverhawk has improved tensioning return of the nut to prevent erratic and excessive bolt loads. Furthermore, the hydraulic nut requires a minimal number of operators and facilitate fast and trouble-free installation – which translates to reduced operations costs.
Thread Diameter “A” | Hydraulic Ram Area | Maximum Hydraulic Load | Nut Height “B” | Nut Diameter “C” | Maximum Stroke | ||||||
---|---|---|---|---|---|---|---|---|---|---|---|
inch | cm | inch | cm | lb | kg | inch | cm | inch | cm | inch | cm |
1.500 | 3.810 | 2.651 | 6.734 | 79,530 | 36,074 | 2.250 | 5.715 | 3.000 | 7.620 | 0.225 | 0.572 |
1.625 | 4.128 | 3.111 | 7.902 | 93,330 | 42,334 | 2.438 | 6.193 | 3.250 | 8.255 | 0.244 | 0.620 |
1.750 | 4.445 | 3.608 | 9.164 | 108,240 | 49,097 | 2.625 | 6.668 | 3.500 | 8.890 | 0.263 | 0.668 |
1.875 | 4.763 | 4.142 | 10.521 | 124,260 | 56,363 | 2.813 | 7.145 | 3.750 | 9.525 | 0.281 | 0.714 |
2.000 | 5.080 | 4.712 | 11.968 | 141,360 | 64,120 | 3.000 | 7.620 | 4.000 | 10.160 | 0.300 | 0.762 |
2.250 | 5.715 | 5.964 | 15.149 | 178,920 | 81,157 | 3.375 | 8.573 | 4.500 | 11.430 | 0.338 | 0.859 |
2.500 | 6.350 | 7.363 | 18.702 | 220,890 | 100,194 | 3.750 | 9.525 | 5.000 | 12.700 | 0.375 | 0.953 |
2.750 | 6.985 | 8.909 | 22.629 | 267,270 | 121,232 | 4.125 | 10.478 | 5.500 | 13.970 | 0.413 | 1.049 |
3.000 | 7.620 | 10.603 | 26.932 | 318,090 | 144,283 | 4.500 | 11.430 | 6.000 | 15.240 | 0.450 | 1.143 |
3.250 | 8.255 | 12.444 | 31.608 | 373,320 | 169,335 | 4.875 | 12.383 | 6.500 | 16.510 | 0.488 | 1.240 |
3.500 | 8.890 | 14.432 | 36.657 | 432,960 | 196,387 | 5.250 | 13.335 | 7.000 | 17.780 | 0.525 | 1.334 |
3.750 | 9.525 | 16.567 | 42.080 | 497,010 | 225,440 | 5.625 | 14.288 | 7.500 | 19.050 | 0.563 | 1.430 |
4.000 | 10.160 | 18.850 | 47.879 | 565,500 | 256,506 | 6.000 | 15.240 | 8.000 | 20.320 | 0.600 | 1.524 |
4.500 | 11.430 | 23.856 | 60.594 | 715,680 | 324,627 | 6.750 | 17.145 | 9.000 | 22.860 | 0.675 | 1.715 |
5.000 | 12.700 | 29.452 | 74.808 | 883,560 | 400,776 | 7.500 | 19.050 | 10.000 | 25.400 | 0.750 | 1.905 |
5.500 | 13.970 | 35.637 | 90.518 | 1,069,110 | 484,940 | 8.250 | 20.955 | 11.000 | 27.940 | 0.825 | 2.096 |
6.000 | 15.240 | 42.412 | 107.726 | 1,272,360 | 577,132 | 9.000 | 22.860 | 12.000 | 30.480 | 0.900 | 2.286 |
6.500 | 16.510 | 49.775 | 126.429 | 1,493,250 | 677,326 | 9.750 | 24.765 | 13.000 | 33.020 | 0.975 | 2.477 |
7.000 | 17.780 | 57.727 | 146.627 | 1,731,810 | 785,535 | 10.500 | 26.670 | 14.000 | 35.560 | 1.050 | 2.667 |
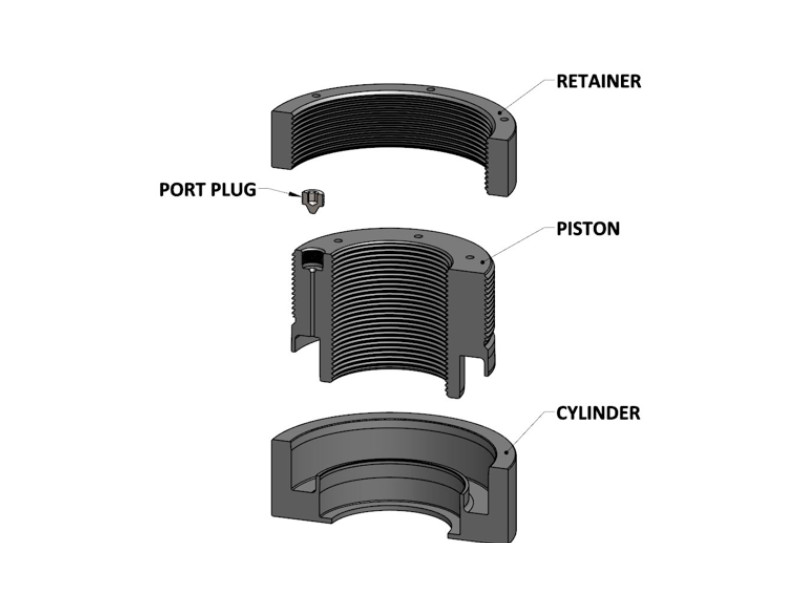
Supports tensioning of multiple bolts concurrently | |
Simultaneous “daisy-chaining” with uniform clamp loads and faster assembly | |
Withstand harsh environments | |
Tolerates applications up to 500°F / 260°C | |
Features water charging for special applications | |
Unique seal design of metal-to-metal | |
Features inherent safety | |
Accommodates confined spaces and envelope restrictions. | |
Forces act along bolt axis rather than through torque reaction arms | |
Compact standard sizes as well as custom Designs |
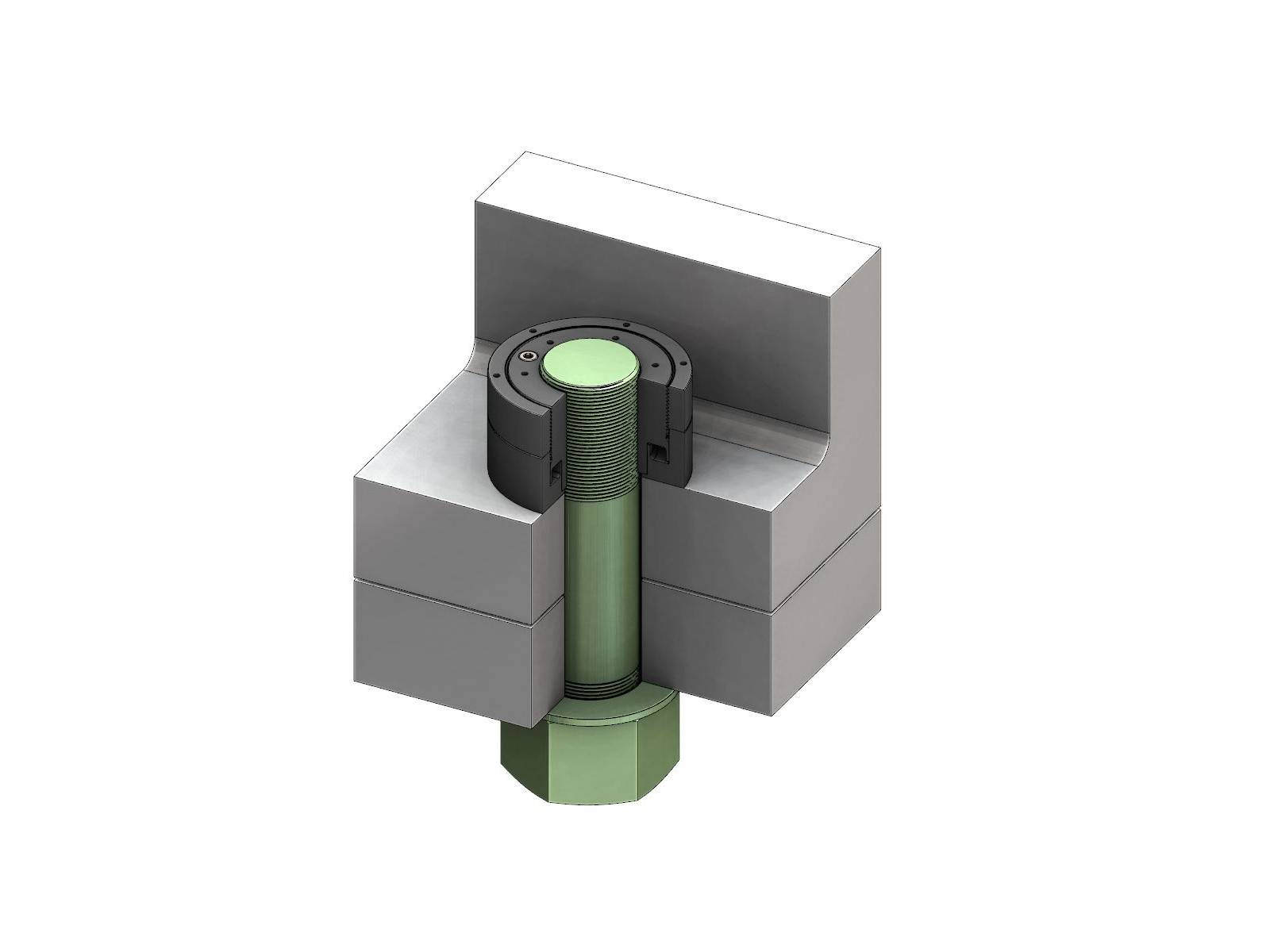
Link multiple tools together for simultaneous tensioning | |
Each individual hydraulic nut is tested at max rated pressure before delivery | |
Every unit comes with a detailed instruction manual | |
Maximum hydraulic load is attained at nut pressure of 30,000 psi / 2,070 bar | |
The retained bolt can load up to 45,000 psi (3100 bar) preload stress in the thread tensile area | |
The alloy steel of the standard models maintains properties up to approx. 500°F / 260°C | |
Custom designs and materials are available if standard design doesn't accomodate your application |
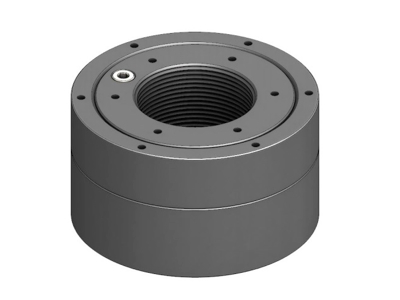
The installation of a hydraulic nut is quite straight forward. Usually, the nut fits within the space of the existing hardware and will not require additional thread length. Screw the hydraulic nut onto the stud and connect it to either a manual or air-driven hydraulic pump using flexible high-pressure hoses.
Pumping oil into the hydraulic nut generates a massive axial force, proportional to the pressure applied, i.e. the higher the hydraulic pressure, the greater a force generated. The force will compress the flanges and stretch the stud, thereby creating a gap between the retainer and cylinder of the hydraulic nut.
The operator turns the retainer down against the cylinder of the nut, which releases the hydraulic pressure. The retainer keeps the stud stretched within its elastic region, countering the stud's tendency to return to the original length. The two counter-acting forces thus create the clamp which holds the joint together. The complete tensioning process can be accomplished within two minutes.